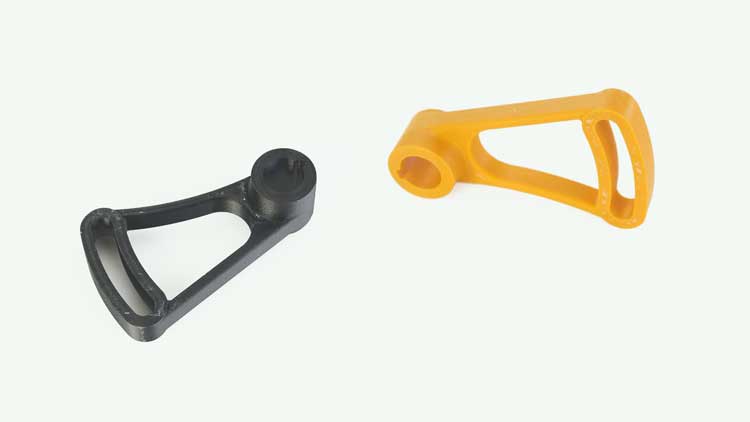
Thermoplastics are well-liked 3D printing materials because, when heated, their chemical properties remain constant. They are simple to melt, layer by layer extrude, and cool to produce models. Thermoplastics, on the other hand, typically have a low melting point and are insufficiently rigid or strong to produce objects that need higher strength. For 3D printed objects to be more mechanically robust, composite materials have been used. Composite materials are stronger, stiffer, more heat resistant, and more durable than conventional thermoplastics (such ABS or PLA), effectively extending the variety of uses for 3D printing.
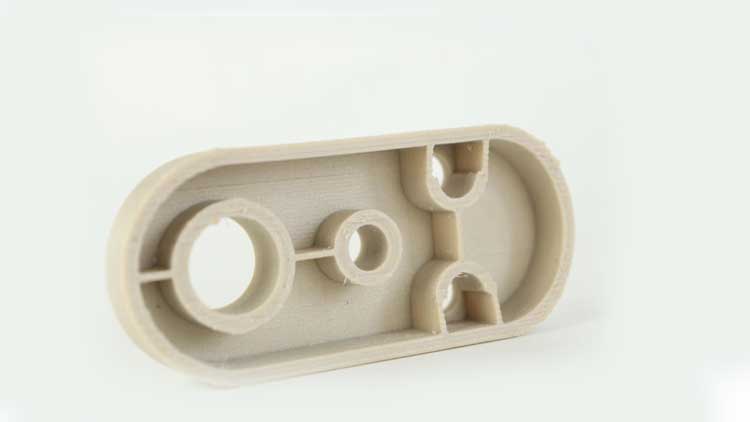
Composite materials, such as polymer, non-metallic, or metal materials, are typically created by combining two or more components. As soon as these materials are combined, they preserve their original properties while also exhibiting brand-new traits. Fiber-reinforced composite materials, such as glass fiber, carbon fiber, and Kevlar, are the most popular types of composite materials utilized in 3D printing.
A base matrix and reinforcing fibers make up a composite material that has been strengthened with fibers (as shown in Figure 2). The composite material’s matrix functions as its core, and the reinforcing material can greatly improve the material’s performance. It could be a scattered, granular, or fiber filler. Nevertheless, as the fibers are fragile and brittle like spaghetti and are likely to break, they are typically wrapped or woven into the matrix material to create a new substance that combines the qualities of the two materials. The fiber-reinforced composite material can be created by 3D printing in either chopped fibers or continuous fibers.
Continuous fibers employ another distinct material mixing method, which is carried out simultaneously during the 3D printing process. The printer normally has two printing nozzles, extruding thermoplastic as the matrix material, and the long fiber coated with curing agent is heated and extruded via another auxiliary nozzle. To directly print the model, the long fiber is fused with the thermoplastic matrix. Continuous Fiber Fabrication is the name of this procedure (CFF). In CFF, similar to sandwich biscuits, long fibers are wrapped in a thermoplastic or resin material and equally dispersed over each layer of the 3D printed product.