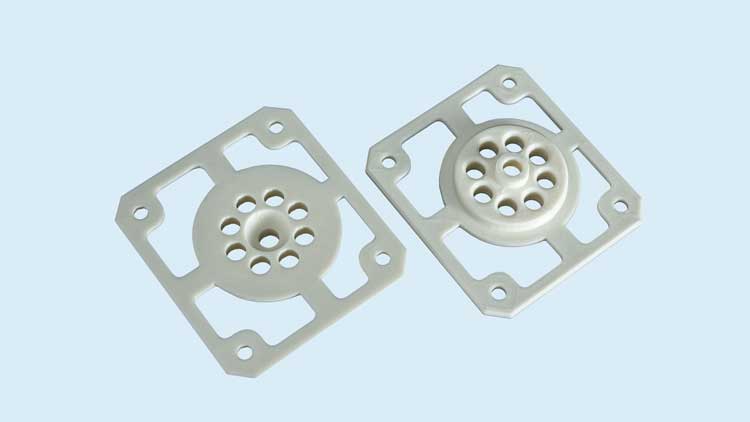
Nylon is utilized in a wide range of products, including the reinforcement of rubber products like car tires and several injection-molded parts for machinery. It is incredibly durable, somewhat resistant to abrasion and moisture absorption, elastic, chemically resistant, strong, and simple to clean. A frequent replacement for low-strength metals is nylon. Its strength, temperature resistance, and chemical compatibility make it the plastic of choice for components in vehicles’ engine compartments.
The terms “PA” (for example, PA 6 or PA 6/66) are frequently used to refer to nylon, which is most frequently seen in the colors black, white, and its natural shade (off-white or beige). Nylon 6/6 is arguably the most often used type for engineering applications. Nylon 6/6 is a suitable plastic for both injection molding and 3D printing and can be extruded (melted and driven through a die). It has a high melting point, making it a great alternative to metal in high-temperature settings (as inside a car’s hood).
- Thermoplastic materials become liquid at their melting point – a very high 220 degrees Celsius in the case of Nylon.
- Instead of burning, thermoplastics like Nylon liquefy, which allows them to be easily injection molded and then subsequently recycled.
- Nylon is often used in gears, bushings, and plastic bearings because of its inherent low-friction properties.
- High performance in other mechanical/chemical/thermal properties make it a good choice for parts that could see a lot of wear.
- Nylon is sometimes filled with a certain percentage of glass fibers to increase its tensile strength.
What are the Disadvantages of Nylon?
Despite having a high melting point, nylon does not hold up well to an open flame. It is a material that burns quickly when exposed to an open flame because it is flammable. The Nylon can be made more flammable by adding flame retardants.UV radiation, particularly from direct sunlight, can also harm nylon. As a result, the material is frequently treated with a UV stabilizer before being injection molded.